Are geotextiles needed for road construction?
In road construction, geotextiles can be used, but this depends on the specific project needs and environmental conditions. Here are some road construction applications where geotextiles may be needed:
Prevent soil erosion: In places such as roadbeds and road slopes, if there is a risk of soil erosion, geotextiles can be used to stabilize the soil and reduce the possibility of erosion. This helps maintain road slope stability and extend the life of the road.
Waterproof layer: In some cases, especially in road projects near wetlands or water sources, geotextiles can be used as a waterproof layer to prevent groundwater from penetrating into the road structure. This reduces the risk of damage to road structures.
Reinforce subgrade: On loose or unstable subgrades, the use of geotextiles can enhance the stability of the subgrade, distribute loads and reduce settlement. This helps increase the carrying capacity of the road.
Isolation layer: In some cases, geotextiles can be used as an isolation layer between the pavement and the underlying soil to prevent interpenetration between different materials and reduce material mixing and maintenance issues.
It should be noted that whether geotextiles need to be used in road construction should be evaluated and decided by engineering designers and professional engineers on a case-by-case basis. The type and specification of geotextile used, as well as the installation method, should be determined according to the project requirements. The correct use of geotextiles can improve the stability, durability and safety of roads.
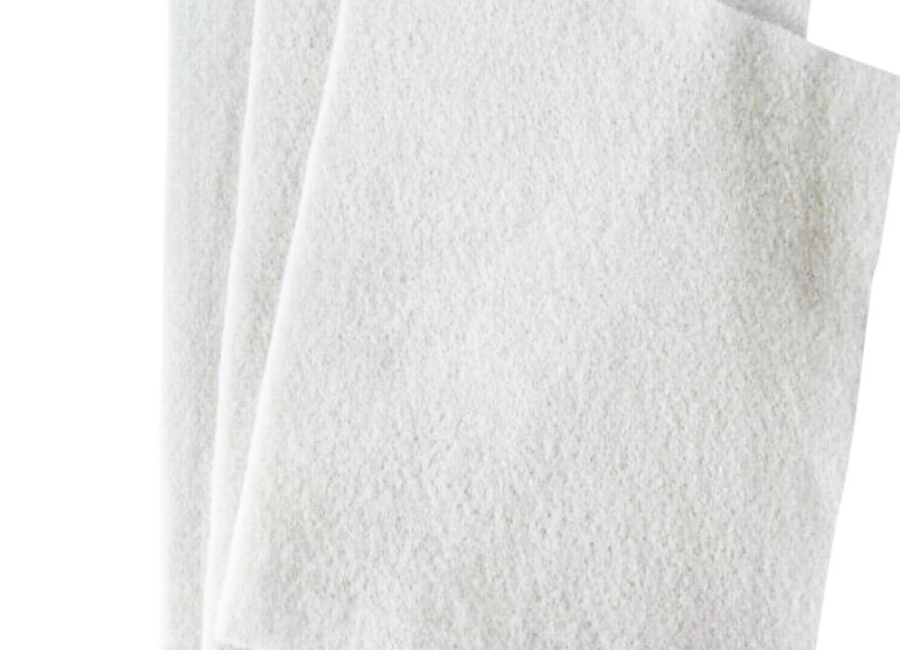
How to install geotextile in road construction?
The installation of geotextiles in road construction is a critical step, helping to enhance road stability, waterproofing and reduce soil erosion. The following are the installation steps of general geotextiles in road construction:
Preparation: Before you begin installing the geotextile, clean and prepare the road foundation. Make sure the surface is flat, dry and clear of sharp objects and obstructions.
Geotextile selection: Select the appropriate type and specification of geotextile based on project requirements and design specifications. Typically, thicker and durable polymer geotextiles such as high-density polyethylene (HDPE) or polypropylene (PP) are used in road construction.
Cutting and laying: Cut the geotextile according to the size required by the design, and then start laying. Make sure the geotextile is flat, wrinkle-free, and laid in strict accordance with the design requirements.
Fixing and Attachment: Geotextiles usually need to be fixed to the ground with ground nails, staples or other fixing devices to prevent them from moving or being blown away by the wind. At seams, use hot melt welding or other suitable joining methods to ensure continuity of the geotextile.
Edge treatment: For the edge of the geotextile, perform appropriate treatment to enhance its stability. Common methods include hemming, reinforcing bands, covering surface fillers, etc.
Covering layer: The covering layer on the road surface is covered with geotextile. This layer can be gravel, asphalt concrete, or other road surface material, depending on the road design and use.
Compaction and adjustment: For the overburden layer, use corresponding mechanical equipment (such as a road roller) to compact and adjust the road surface to ensure it is uniform and stable.
Quality control: Carry out quality control and inspection to ensure that the laying quality, fixation and connection of the geotextile meet the design and specification requirements.
Maintenance and Monitoring: Regularly monitor road conditions to ensure the geotextile continues to perform its role. When necessary, maintenance and repairs are performed to ensure the performance of the road.
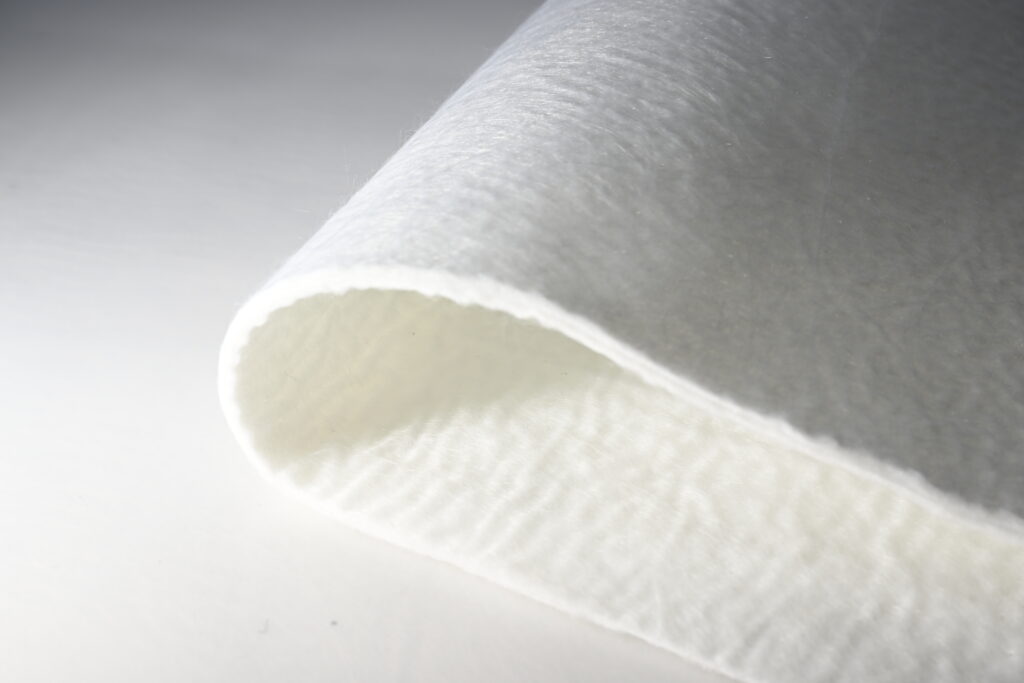
Which geotextile should be chosen for road construction?
It is very important to choose the appropriate type of geotextile in road construction because different types of geotextile have different characteristics and application ranges. The choice of geotextile should be determined based on the specific needs and environmental conditions of the road project. Here are some common geotextile types and their suitability for use in road construction:
High-density polyethylene (HDPE) geotextile: HDPE geotextile is a high-density polyethylene film with good chemical stability and mechanical strength. It is commonly used for road anti-seepage, waterproofing and soil stability enhancement. It excels as a waterproofing layer, impermeable layer and soil barrier.
Polypropylene (PP) geotextile: Polypropylene geotextile is highly resistant to chemical corrosion and is suitable for environments where chemicals are present. It is used in soil isolation, waterproofing and anti-seepage applications in road construction.
Polyvinyl Chloride (PVC) Geotextiles: PVC geotextiles are commonly used in large road and highway projects for their weather resistance and anti-corrosion properties. It can be used for soil isolation, waterproofing and anti-seepage.
Composite Geotextiles: Composite geotextiles are typically composed of different types of polymer materials and have a multi-layer structure that can combine multiple properties. This makes them flexible and adaptable in a variety of road construction applications.
Non-woven geotextiles: Non-woven geotextiles are usually made of polymer fiber materials and have good resistance to penetration and tearing. They are commonly used for soil stabilization and preventing turf growth applications.
When choosing a geotextile, you need to consider the following factors:
Soil type and characteristics
Groundwater situation
Expected traffic volumes and loads
Environmental conditions (such as the presence of chemicals)
budget constraints