How to optimize geomembrane construction?
Optimizing geomembrane construction involves a combination of meticulous planning, efficient resource management, adherence to quality standards, and leveraging advanced technologies. Here are some strategies to achieve optimization:
1. Detailed Planning and Design
Comprehensive Site Assessment: Conduct thorough site assessments including soil tests, topographical surveys, and environmental impact studies.
Precise Engineering Design: Develop detailed engineering designs that consider site-specific conditions and intended use of the geomembrane.
Clear Specifications: Establish clear material and construction specifications, including thickness, type of geomembrane, and seam strength requirements.
2. Quality Materials and Equipment
High-Quality Geomembranes: Use high-quality geomembrane materials suitable for the specific application (e.g., HDPE, LLDPE, PVC).
Advanced Equipment: Utilize state-of-the-art installation equipment for precise placement, welding, and testing.
Proper Storage: Store geomembrane rolls properly to avoid damage before installation.
3. Skilled Workforce
Experienced Installers: Hire experienced and certified installers who are familiar with best practices and the latest installation techniques.
Continuous Training: Provide ongoing training for the installation crew to stay updated on new technologies and methods.
4. Efficient Installation Processes
Pre-Installation Preparation: Ensure the site is well-prepared, with a smooth and stable subgrade free of sharp objects and debris.
Weather Considerations: Plan installation during favorable weather conditions to avoid issues related to temperature, wind, and precipitation.
Seam Quality Control: Use automated welding equipment and conduct regular destructive and non-destructive testing of seams.
5. Advanced Technologies
GPS and Drones: Use GPS for precise layout and drones for site monitoring and progress tracking.
Automated Systems: Implement automated welding machines for consistent and high-quality seams.
Real-Time Monitoring: Use real-time monitoring systems to track installation parameters and environmental conditions.
6. Environmental and Safety Considerations
Dust and Emission Control: Implement dust suppression and emission control measures to minimize environmental impact.
Safety Protocols: Follow stringent safety protocols to protect workers and ensure compliance with health and safety regulations.
Waste Management: Establish effective waste management practices to handle offcuts and other construction debris.
7. Quality Assurance and Control
Regular Inspections: Conduct regular inspections throughout the installation process to ensure compliance with design and material specifications.
Testing: Perform rigorous testing of seams, including peel and shear tests, to verify integrity.
Documentation: Maintain detailed records of installation procedures, test results, and inspections for accountability and future reference.
8. Project Management
Efficient Scheduling: Develop an efficient project schedule that minimizes delays and coordinates various activities seamlessly.
Resource Allocation: Ensure optimal allocation of resources, including labor, materials, and equipment, to avoid bottlenecks.
Communication: Maintain clear and continuous communication among all stakeholders, including project managers, engineers, installers, and clients.
9. Sustainability Practices
Eco-Friendly Materials: Use environmentally friendly materials and construction practices.
Energy Efficiency: Optimize energy use by employing efficient equipment and minimizing idle times.
Recycling and Reuse: Implement recycling and reuse practices for geomembrane scraps and other materials.
10. Post-Installation Review
Final Inspection: Conduct a comprehensive final inspection to ensure all aspects of the installation meet the required standards.
As-Built Documentation: Prepare detailed as-built documentation for future reference and maintenance.
Maintenance Plan: Develop a maintenance plan to ensure the long-term performance and integrity of the geomembrane system.
By following these strategies, geomembrane construction can be optimized to ensure efficiency, quality, and sustainability, resulting in a successful and durable installation.
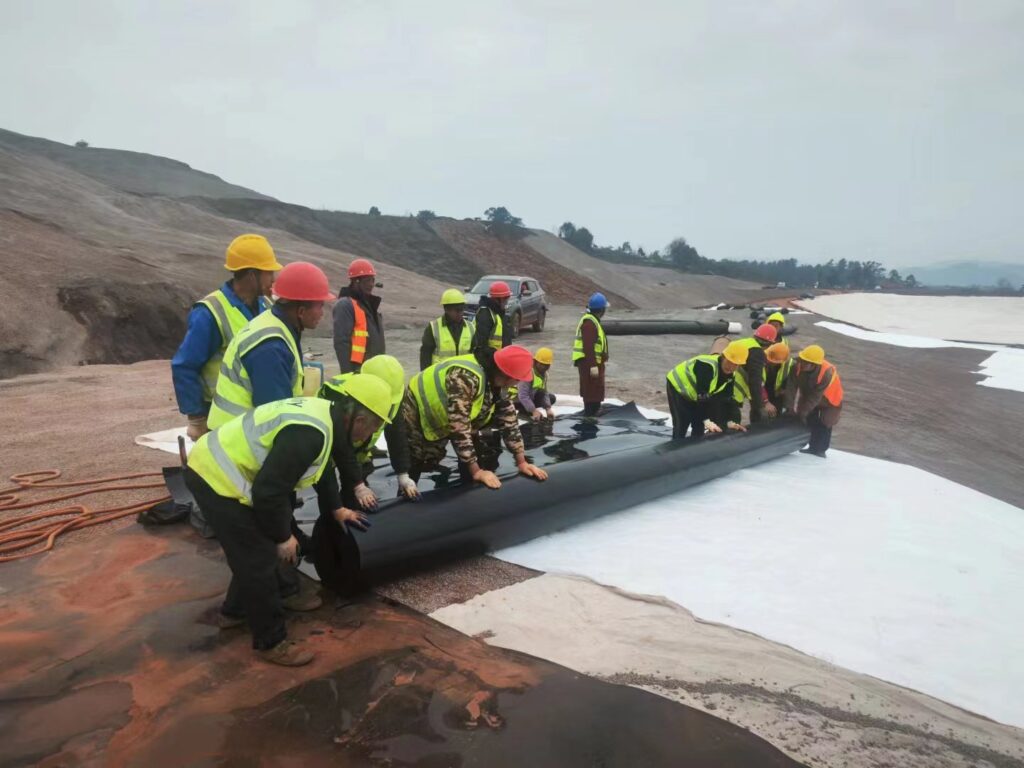
What is the impact of groundwater on geomembrane construction
Groundwater can significantly impact geomembrane construction in several ways, influencing the installation process, the integrity of the geomembrane, and the long-term performance of the containment system. Understanding these impacts and implementing appropriate mitigation measures is crucial for successful geomembrane installation. Here are the key effects of groundwater on geomembrane construction and strategies to manage them:
1. Site Preparation Challenges
Subgrade Stability: High groundwater levels can lead to subgrade instability, making it difficult to achieve a smooth and firm surface for geomembrane placement. This can cause wrinkles, folds, and uneven seams.
Pumping and Dewatering: Managing high groundwater requires dewatering, which can be time-consuming and costly. Proper dewatering techniques must be employed to create a dry and stable working environment.
2. Seepage and Uplift Pressure
Seepage: Groundwater seepage can lead to hydrostatic pressure beneath the geomembrane, causing it to lift or float. This pressure can create bubbles or voids, compromising the integrity of the liner.
Uplift Pressure: Continuous groundwater pressure can cause geomembrane uplift, especially if the groundwater level rises above the geomembrane. This can lead to structural failure or damage to the liner.
3. Chemical Interactions
Chemical Contamination: Groundwater can contain chemicals that may interact with the geomembrane material, potentially leading to degradation or reduced performance over time.
pH Levels: Extreme pH levels in groundwater can affect the durability of certain geomembrane materials, necessitating the selection of chemically resistant materials.
4. Installation and Welding Issues
Difficult Working Conditions: High groundwater levels can create wet and muddy conditions, complicating the installation process and increasing the risk of installation errors.
Welding Challenges: Wet or humid conditions can affect the quality of geomembrane welding, making it difficult to achieve strong and consistent seams.
Mitigation Strategies
Site Preparation and Dewatering
Effective Dewatering Systems: Implement dewatering systems such as sump pumps, wellpoints, or drainage trenches to lower the groundwater level during construction.
Proper Subgrade Preparation: Ensure thorough compaction and stabilization of the subgrade. Use geotextiles or other stabilization materials if necessary.
Design Considerations
Anchor Trenches: Design anchor trenches to hold the geomembrane in place and counteract uplift pressures.
Ballasting: Use ballast materials such as gravel or sand on top of the geomembrane to provide additional weight and counteract buoyancy forces.
Material Selection
Chemical-Resistant Geomembranes: Choose geomembrane materials that are resistant to chemical interactions with local groundwater constituents, such as HDPE or specialized polymer blends.
Thickness and Type: Select appropriate thickness and type of geomembrane based on the groundwater conditions and expected chemical exposure.
Quality Control and Monitoring
Regular Inspections: Conduct regular inspections during and after installation to detect and address any issues related to groundwater impact.
Seam Testing: Perform rigorous seam testing, including vacuum testing and destructive testing, to ensure the integrity of welds in wet conditions.
Long-Term Monitoring and Maintenance
Groundwater Monitoring: Install groundwater monitoring wells around the geomembrane installation site to track groundwater levels and chemical composition over time.
Maintenance Plan: Develop a maintenance plan that includes regular inspection of the geomembrane and associated drainage systems to ensure long-term performance and address any groundwater-related issues promptly.
By understanding the impact of groundwater on geomembrane construction and implementing these mitigation strategies, you can enhance the durability and effectiveness of the geomembrane installation, ensuring it performs as intended over its lifespan.