Sewing requirements for geotextile bags
All stitching must be continuous, eg spot stitching is not permitted. Geotextiles must overlap a minimum of 150mm before overlapping. The minimum stitch distance from the selvage (the exposed edge of the material) is at least 25mm.
The seamed geotextile seams include one row of seams and chain seams. The thread used for suturing should be a resin material with a minimum tension exceeding 60N, and have chemical resistance and UV resistance comparable to or exceeding that of geotextiles.
Any “missing stitches” in the sewn geotextile must be resewn in the affected area.
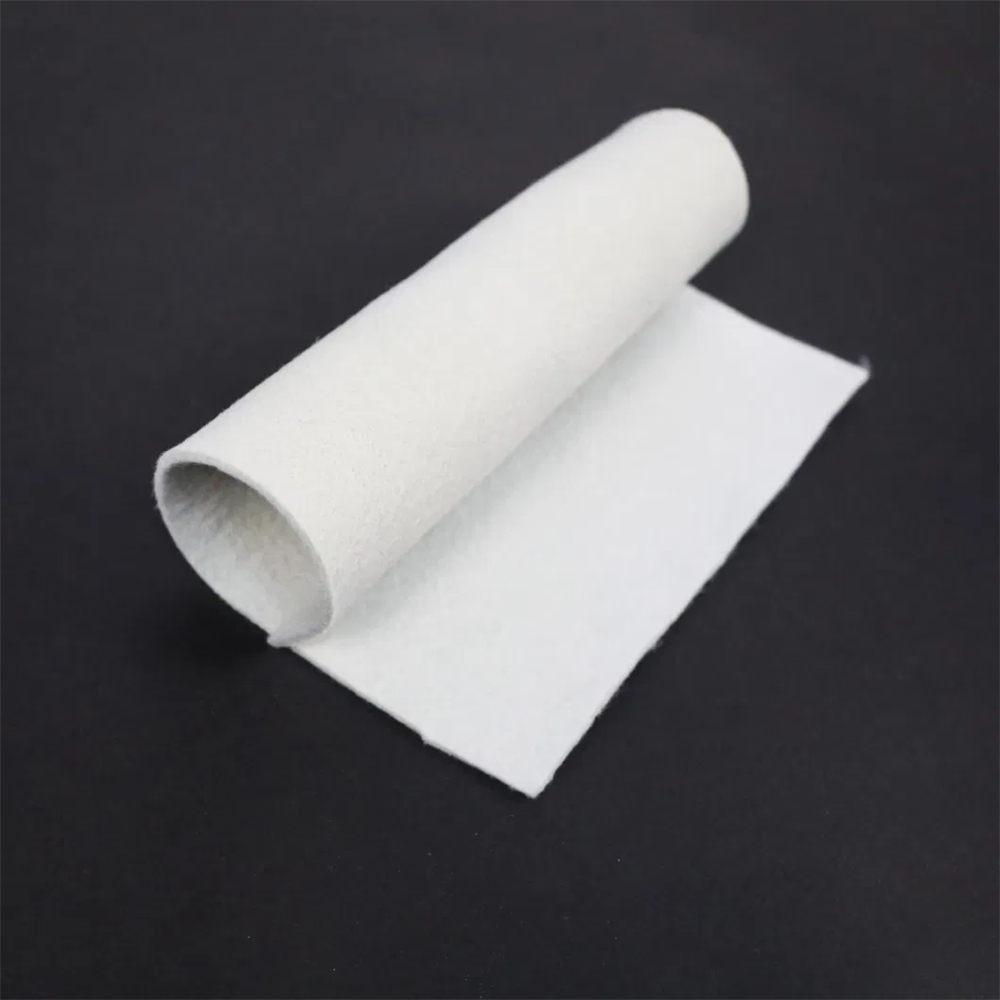
Geotextile quality testing standards
Geotextile quality testing standards include appearance quality, physical performance and chemical performance testing.
Appearance quality: Geotextiles are not allowed to have holes, cracks, broken roots, hard lumps, impurities, oil stains, joints, color differences, spots, missing wefts, shrinkage, uneven tightness and other defects.
Physical performance testing: including tensile strength, tearing strength, bursting strength, peeling strength, abrasion resistance, aging resistance, bioerosion resistance and other indicators.
Chemical performance testing: including chemical corrosion resistance, biological corrosion resistance and other indicators.
Geotextile bag production process
Material preparation: Prepare high-strength and permeable geotextiles, as well as other necessary auxiliary materials.
Cutting: Cut the geotextile into corresponding shapes and sizes according to actual needs.
Sewing: Use a sewing machine to sew the cut geotextile into a geotextile bag.
Filling: Fill the prepared geotextile bag with an appropriate amount of soil, sand and other materials.
Closure: Seal the opening of the geotextile bag to ensure its water resistance and durability.