What are the properties of geo membrane?
Geomembranes are synthetic liners or barriers used in various civil engineering, environmental, and containment applications. They are typically made from polymeric materials such as high-density polyethylene (HDPE), low-density polyethylene (LDPE), polyvinyl chloride (PVC), and ethylene propylene diene monomer (EPDM). The properties of geomembranes can vary depending on the specific material and manufacturing process, but some common properties include:
Thickness: Geomembranes come in a range of thicknesses, typically measured in millimeters. Thicker geomembranes offer greater resistance to punctures and mechanical stresses.
Strength and Durability: Geomembranes exhibit high tensile strength and tear resistance to withstand loads and stresses during installation and throughout their service life. They are designed to maintain their integrity under various environmental conditions, including exposure to chemicals, UV radiation, and temperature fluctuations.
Flexibility: Geomembranes are flexible and can conform to irregular surfaces and contours, making them suitable for lining applications in ponds, landfills, reservoirs, and other structures with complex geometries.
Chemical Resistance: Geomembranes are resistant to a wide range of chemicals, including acids, bases, solvents, and hydrocarbons. This property is crucial for applications involving containment of hazardous waste, industrial effluents, and other potentially harmful substances.
Impermeability: Geomembranes provide an impermeable barrier to fluids and gases, preventing the migration of contaminants into the surrounding environment or groundwater. They are used to line landfills, ponds, lagoons, and other containment facilities to prevent leakage and pollution.
UV Resistance: Some geomembranes are formulated with additives or coatings to enhance their resistance to UV radiation and prolong their service life in outdoor applications.
Seam Strength: Geomembranes can be fabricated in large panels and seamed together using various welding or adhesive techniques. The strength and integrity of the seams are critical for maintaining the overall effectiveness of the geomembrane liner.
Temperature Resistance: Geomembranes can withstand a wide range of temperatures, from freezing conditions to high temperatures encountered in hot climates or industrial processes.
These properties make geomembranes an essential component in environmental protection, water conservation, waste containment, and infrastructure development projects. Proper selection, installation, and maintenance of geomembranes are essential to ensure long-term performance and reliability.

How thick is a geomembrane?
The thickness of a geomembrane can vary depending on the specific application and requirements of the project. Geomembranes are available in a wide range of thicknesses, typically measured in millimeters (mm) or sometimes in mils (1 mil = 0.0254 mm).
For example, geomembranes used in relatively simple applications such as decorative ponds or temporary erosion control measures may be relatively thin, ranging from 0.5 mm to 1.0 mm (20 mils to 40 mils).
On the other hand, geomembranes used in more demanding applications such as landfill liners, liquid containment facilities, or industrial ponds may be much thicker, typically ranging from 0.75 mm to 3.0 mm (30 mils to 120 mils) or even thicker in some cases.
The choice of geomembrane thickness depends on factors such as the expected service life of the liner, the type and severity of environmental conditions, the potential for mechanical stresses, and the requirements for impermeability and chemical resistance.
It’s important to consult with a geotechnical engineer or other qualified professional to determine the appropriate thickness of geomembrane for a specific project based on site-specific conditions and performance criteria.
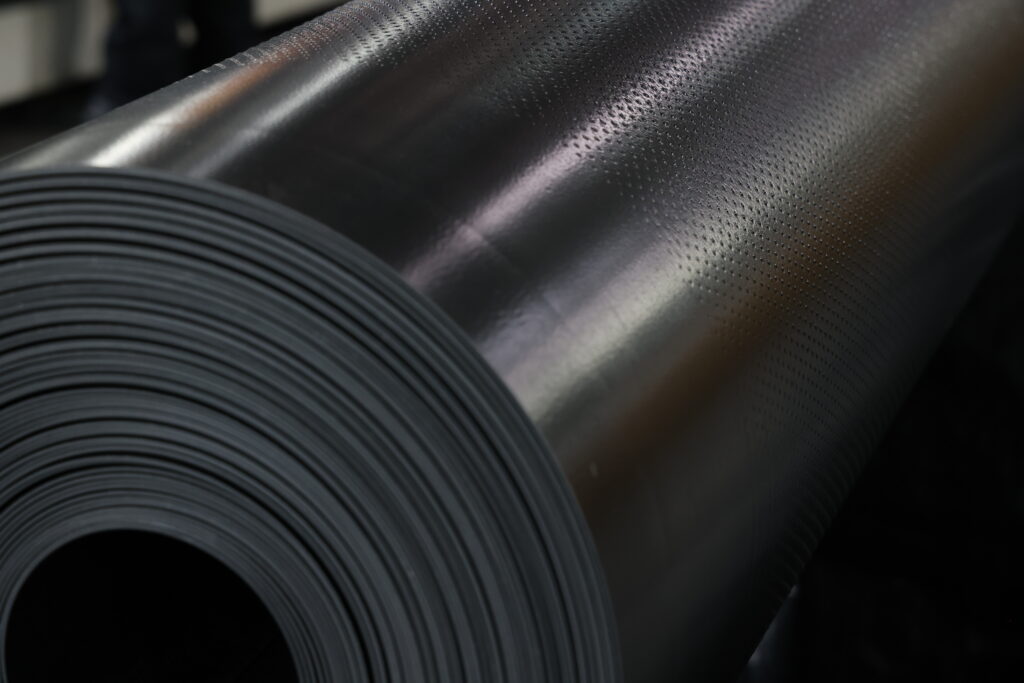
How is geomembrane manufactured?
Geomembranes are manufactured through a process that involves extrusion or calendering, depending on the type of material being used. The most common materials used for geomembranes are high-density polyethylene (HDPE), low-density polyethylene (LDPE), polyvinyl chloride (PVC), and ethylene propylene diene monomer (EPDM). Here’s a general overview of the manufacturing process for geomembranes:
Material Preparation: The raw polymer resin is first processed and compounded with additives such as antioxidants, stabilizers, UV inhibitors, and colorants to enhance the material’s properties and performance.
Extrusion or Calendering: The compounded resin is then fed into an extruder or calendering machine, where it undergoes heating and pressure to melt and form a continuous sheet of geomembrane.
Extrusion: In the extrusion process, the molten resin is forced through a die to produce a continuous sheet of geomembrane with a uniform thickness. The extruded sheet may then be cooled and rolled onto large spools for further processing.
Calendering: In the calendering process, the molten resin is passed through a series of heated rollers to form a continuous sheet of geomembrane with a consistent thickness. The calendered sheet may undergo additional cooling and treatment before being wound onto rolls.
Surface Treatment: The geomembrane may undergo surface treatment processes such as corona treatment or chemical priming to improve adhesion and facilitate welding or seaming during installation.
Quality Control: Throughout the manufacturing process, quality control measures are implemented to ensure that the geomembrane meets the required specifications and standards for thickness, strength, flexibility, impermeability, and other performance criteria.
Finishing and Packaging: Once the geomembrane has been produced and inspected, it may be cut to the desired dimensions and packaged for shipment to construction sites or distribution centers.
The manufacturing process for geomembranes requires precision and attention to detail to produce high-quality liners that can effectively serve their intended purposes in various civil engineering, environmental, and containment applications. Different manufacturers may employ variations of the process depending on the specific requirements of their products and the materials being used.