How to lay hdpe geomembrane?
The HDPE geomembrane process is the most critical process in the entire anti-seepage system. The success or failure of the entire project depends on the construction quality of the artificial anti-seepage layer.
Before laying the HDPE geomembrane, the geomembrane installation unit must provide the geomembrane laying and welding layout plan. It is required to choose the laying direction reasonably, reduce the stress on the joints as much as possible, and rationally arrange the position of each piece of material to minimize the joints. There shall be no transverse joints on the slope with a slope of 10% and within 1.5m of the toe of the slope.
Before laying the HDPE geomembrane, the owner and the supervising engineer should jointly conduct a comprehensive confirmation of the site conditions to ensure that the foundation surface of the landfill is smooth, without unevenness, sharp particles, and various hard particles that may damage the HDPE geomembrane. If debris exists, there should be no harmful debris within 25mm of the surface depth. The quality of the anti-seepage material (various performance indicators, whether there are bubbles, holes, wrinkles on the surface, etc.) should be strictly inspected. Laying can be carried out after confirmation.
The HDPE geomembrane should be laid smoothly and firmly, with as few wrinkles as possible. After laying, it should be ballasted and anchored in time. The HDPE geomembrane should be laid with the smooth side up and the rough side down. During the construction process, the influence of climate factors should be fully considered and allowances should be made for thermal expansion. The length of cold shrinkage.
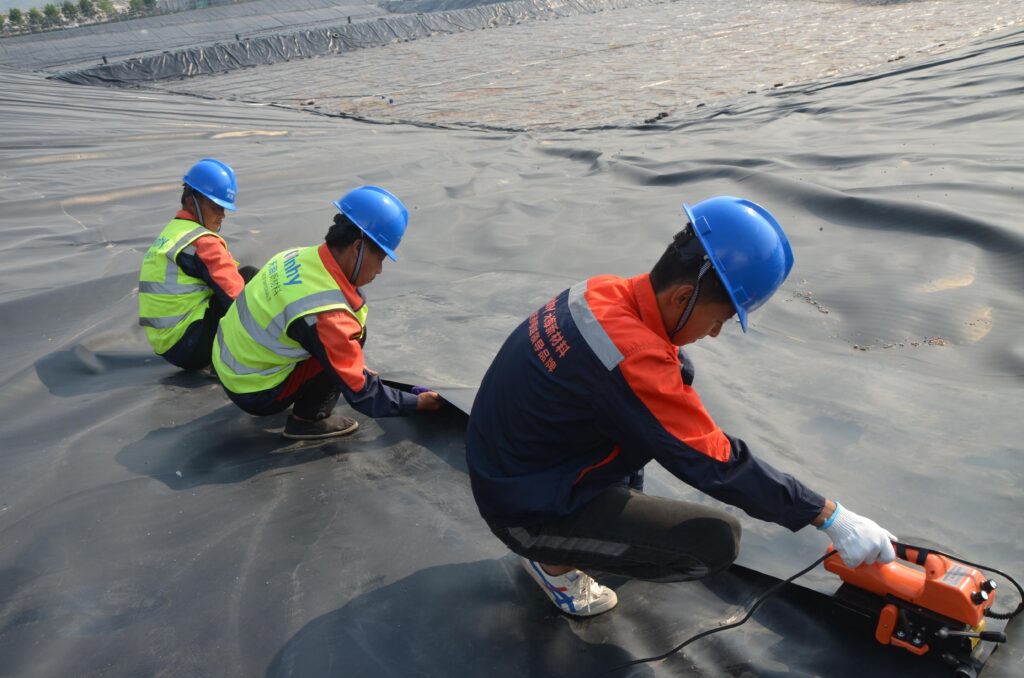
How to lay composite geomembrane?
Before laying the composite geomembrane, a supervisory engineer should be asked to conduct a comprehensive confirmation of the site conditions to ensure that the foundation surface of the landfill area is smooth, free of unevenness, cracks, sharp particles, hard debris, etc., and that there is no possibility of damaging the geomembrane. All kinds of foreign matter, and the quality of the anti-seepage material (knowledge performance refers to whether there are bubbles, holes, wrinkles, damage, etc. on the surface) shall be strictly inspected and laid only after confirmation.
2. The sampling for acceptance inspection of composite geomembranes should be based on the continuous production of products of the same brand of raw materials, the same formula, the same specifications, and the same process. The inspection items should be carried out according to the performance content of the composite geomembrane, and whether there is any damage, breakage, etc. during transportation. phenomenon, product identification must be verified.
3. Each roll of material laid should be numbered and laid in order. The composite geomembrane shall be numbered and archived by the supervision engineer for inspection.
4. The geomembrane materials constructed on site should not be exposed for a long time and should be kept away from fire sources.
5. During the laying process, workers are not allowed to wear shoes that may damage the composite geomembrane, and are not allowed to smoke or engage in other activities that can damage the composite geomembrane at the laying site.
6. Before laying the composite geomembrane, attention should be paid to the forward and reverse directions of laying. When laying, the dragging of the composite geomembrane on the foundation should be minimized to avoid damage to the composite geomembrane. If necessary, a temporary layer can be placed on the ground. Geotechnical materials to reduce friction.
7. The laid anti-seepage materials should be placed in soil bags promptly to prevent them from being blown away by the wind.
8. Outdoor construction of geomembrane should be carried out when the temperature is above 5℃, the wind force is below Level 4, and there is no rain or snow.
9. No vehicles are allowed to drive directly on composite geomembranes and non-woven fabrics.
10. In order to avoid shrinkage, wrinkles or stress in the material due to temperature changes, the laid composite geomembrane should be welded in time after obtaining the consent of the supervision engineer. After passing the inspection, protective materials should be laid.
11. During the welding construction process of the composite geomembrane, the supervision engineer should be promptly requested to inspect the operating procedures, laying and welding quality. If any quality problems are found, they should be repaired in time.
12. There should be no tree roots, stones and larger particles in the anchoring trench of the middle platform of the composite geomembrane and the anchoring trench on the slope top. They should be smoothed and compacted.
13. Composite geomembrane welding position and welding technology requirements:
(1) When welding the composite geomembrane on the slope, the overlap joint should be parallel to the direction of the slope, and the transverse overlap joint position of the slope should be more than 1.0 meters away from the edge of the bottom of the slope.
(2) Official welding shall not begin until the sample welded by the welding equipment has passed the trial welding inspection or been confirmed by the supervision engineer.
(3) Before welding, the surface of the geomembrane must be cleaned of dust, dirt and other foreign matter.
(4) The overlap between the two welded geomembranes shall not be less than 10 cm.
(5) When the temperature is lower than 5℃ or higher than 40℃, the construction unit should provide written instructions on the welding quality equivalent to that within the specified temperature range, and ask the supervising engineer for confirmation before proceeding with construction.
(6) The geomembrane welding method adopts double weld overlap, and extrusion welding is used for repairs (such as repairing holes) where the fusion welding equipment cannot reach.
(7) The connection strength of the geomembrane weld should be greater than the strength of the parent material.
14. The construction site should have sufficient welding equipment to ensure continuous welding construction.
15. A testing laboratory should be set up at the construction site and equipped with necessary testing equipment, and on-site testing should conduct non-destructive tests (such as inflation and vacuum tests, etc.) and destructive tests (such as shear peeling) on the composite geomembrane welds. test, etc.).
16. On-site inspection of geomembrane welding is completed. All holes in the inflatable raincoat made during the inspection should be plugged immediately using the extrusion welding method.
17. Welding joints that are weak or missing should be repaired in time, and the repaired welding parts should be vacuum inspected.
18. The construction unit must have a complete construction organization plan and reasonably arrange the materials according to the size of the composite geomembrane at the construction site to reduce the loss of the geomembrane.
Safety disclosure content:
1. When entering the site, you must comply with Chinalco’s ten prohibitions on production safety.
2. Operators must be trained and abide by operating safety regulations. You must wear safety protective equipment as required, abide by rules and disciplines, and obey instructions.
3. Operators are strictly prohibited from operating under the influence of alcohol or entering the site without safety protective equipment.