What is the production process of geomembrane?
Raw material preparation: select high-density polyethylene (HDPE) or linear low-density polyethylene (LLDPE) as the raw material, and send it into the extruder after screening, cleaning, drying and other treatments.
Extrusion molding: The pretreated raw materials are fed into the extruder, heated and melted, and extruded from the head of the extruder to form a film. The temperature, pressure, speed and other parameters of the extruder need to be adjusted according to different materials and thicknesses.
Cooling and cutting: The extruded geomembrane needs to be cooled, usually by cooling rolls or water. Cut the cooled geomembrane to the required size and shape.
Inspection and packaging: Inspect the geomembrane, including thickness, density, tensile strength, puncture strength and other indicators. Geomembranes that meet standard requirements are packaged, usually in rolls or folded packages.
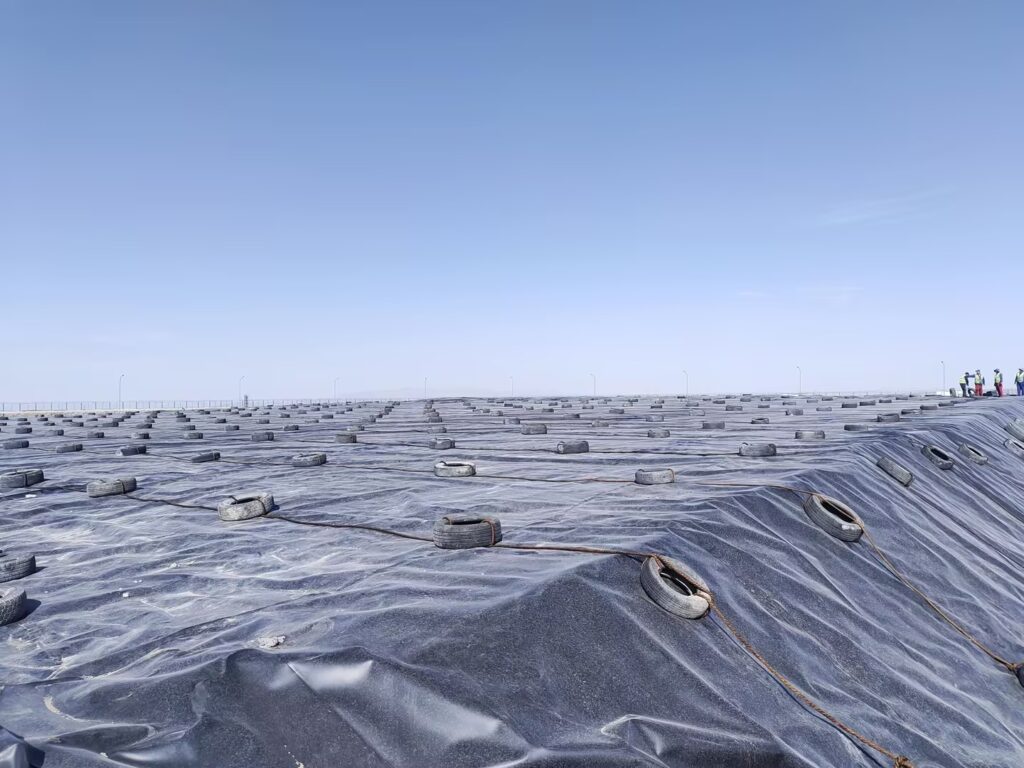
What are the dimensions of geomembrane?
The size specification of geomembrane is mainly distinguished by width and length.
Common width sizes are 1.0m, 1.5m, 2.0m, 2.5m, 3.0m, etc. There is no limit to the length, and can be cut arbitrarily according to actual needs. In practical applications, the dimensions and specifications of the geomembrane should be determined according to the needs of specific projects.
What are the types of geomembranes?
Geomembranes can be divided into HDPE geomembranes, LDPE geomembranes, ECB geomembranes, and PVC geomembranes according to the production raw materials. Among them, HDPE geomembranes are the mainstream design in anti-seepage projects.
HDPE geomembrane has excellent heat resistance and cold resistance, good chemical stability, high rigidity and toughness, and good mechanical strength. Its raw material is high-density polyethylene, which is mostly used in anti-seepage projects such as landfills and tailings storages.
The raw material of LDPE geomembrane is low-density polyethylene, which also has good weather resistance, chemical corrosion resistance, water resistance and air tightness. It has strong flexibility and impact resistance, non-toxic and tasteless, and is suitable for anti-seepage projects such as water conservancy. .
The raw material of ECB geomembrane is ethylene vinyl acetate copolymer, which has excellent flexibility, cold resistance, elasticity, stress cracking resistance and light specific gravity, and is especially suitable for waterproof material on the inner surface of the vault.
The original material of PVC geomembrane is polyvinyl chloride, which is mostly used in building materials.
In addition, there are LLDPE geomembranes and EVA geomembranes, both of which have different characteristics and scope of application. The selection of the appropriate geomembrane type should be determined based on actual project needs.
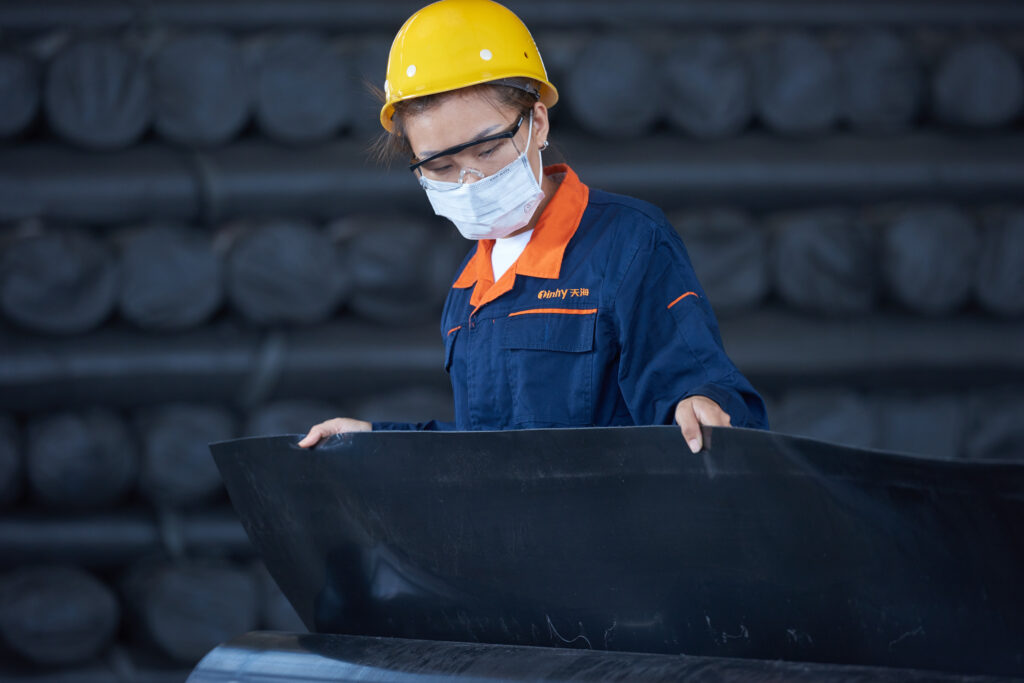
HDPE geomembrane welding steps
Clean the geomembrane welding surface to ensure it is smooth, dust-free and oil-free.
Connect the welding machine plug to the socket of the welding machine and adjust the temperature of the welding machine to 270°C.
Align the edges of the two geomembrane materials that need to be welded, and use a welding machine to continuously weld on their surfaces. The welding width is 10~12mm, and the length of the welding line is not more than 10mm.
During the welding process, the molten residue on the surface of the welding seam should be removed in time to keep the welding surface clean.
After the welding is completed, the quality of the welding seam should be checked to ensure that the welding seam is smooth, defect-free and has good sealing.