Why does metal need a geomembrane?
Metals need geomembranes during extraction, processing, and waste management to prevent environmental contamination and to ensure the safety and efficiency of mining operations. Here are the primary reasons why geomembranes are essential in metal mining:
Containment of Leachates:
- Many metals are extracted using chemical leaching processes, where chemicals such as cyanide (for gold) or sulfuric acid (for copper) are used to dissolve the metal from the ore. Geomembranes line leach pads to contain these chemicals and prevent them from leaching into the soil and groundwater.
Environmental Protection:
- Geomembranes act as barriers that prevent toxic substances from contaminating surrounding ecosystems. This is crucial in protecting water bodies, soil, and wildlife from the harmful effects of metal mining byproducts and chemicals.
Groundwater Protection:
- By preventing the seepage of hazardous materials into the groundwater, geomembranes help maintain the quality of local water supplies. This is vital for communities relying on groundwater for drinking, agriculture, and other uses.
Regulatory Compliance:
- Mining operations must comply with stringent environmental regulations that mandate the use of containment systems to manage waste and leachates. Geomembranes help mining companies meet these legal requirements and avoid fines, legal actions, and shutdowns.
Operational Efficiency:
- Geomembranes help create controlled environments for chemical leaching and tailings storage, improving the efficiency and effectiveness of metal recovery processes. They also help manage and contain waste, making it easier to handle and process.
Tailings Management:
- Tailings, the waste materials left after the metal is extracted from the ore, can contain harmful chemicals and heavy metals. Geomembranes line tailings ponds and storage facilities to prevent the release of these contaminants into the environment.
Prevention of Acid Mine Drainage:
- Certain mining activities can lead to the formation of acid mine drainage (AMD), where sulfide minerals in waste rock and tailings react with water and air to form sulfuric acid. Geomembranes help contain and manage AMD, preventing it from contaminating water sources.
Longevity and Durability:
- Geomembranes are designed to withstand harsh chemical environments and physical stress, providing long-term containment solutions that reduce the risk of leaks and failures over time.
By providing a reliable barrier, geomembranes are critical in ensuring that metal mining operations do not adversely impact the environment and public health.
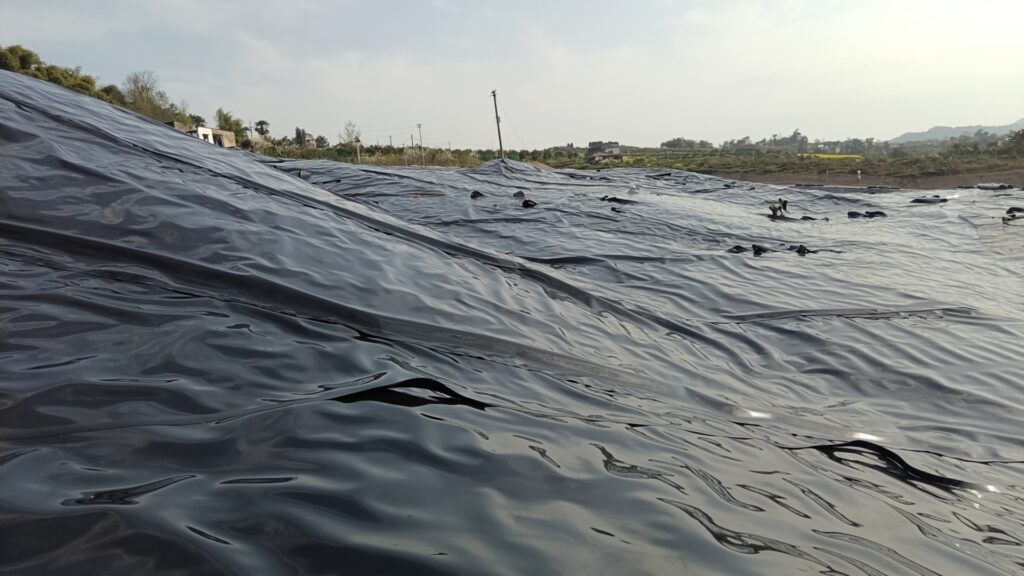
Which metals require geomembranes?
Geomembranes are often used in the mining industry to contain and manage various types of metals during extraction, processing, and waste management. Here are some metals that typically require the use of geomembranes:
Gold: Gold mining operations frequently use geomembranes to line heap leach pads, which help contain the cyanide solution used to extract gold from ore. Geomembranes prevent the leachate from contaminating the surrounding environment.
Copper: Similar to gold mining, copper mining often employs geomembranes in heap leaching operations. Geomembranes help contain the sulfuric acid solutions used to leach copper from ore, preventing environmental contamination.
Uranium: Uranium mining operations use geomembranes to line tailings ponds and heap leach pads. Geomembranes help contain radioactive materials and prevent groundwater contamination.
Nickel: Nickel mining operations utilize geomembranes in tailings storage facilities and heap leach pads to manage acidic leachate and prevent environmental contamination.
Zinc: Zinc mining operations often use geomembranes in tailings storage facilities and heap leaching processes. Geomembranes help contain and manage the acidic solutions used in zinc extraction.
Silver: Silver mining, often associated with gold mining, also uses geomembranes in heap leach pads and tailings ponds to contain leachate solutions and prevent environmental contamination.
Lithium: Lithium extraction processes, particularly those involving brine, use geomembranes to line evaporation ponds. Geomembranes help contain the lithium-rich brine and prevent leakage into the environment.
Lead: Lead mining operations use geomembranes in tailings storage facilities to prevent the leaching of lead and other heavy metals into the surrounding environment.
Iron: Iron ore mining can involve geomembranes in tailings storage facilities to contain mine tailings and prevent the release of contaminants into the environment.
In all these cases, geomembranes provide a barrier to protect soil and groundwater from contamination by toxic leachates and other hazardous substances. The use of geomembranes is crucial in ensuring environmental compliance and protecting ecosystems from the potentially harmful effects of mining activities.
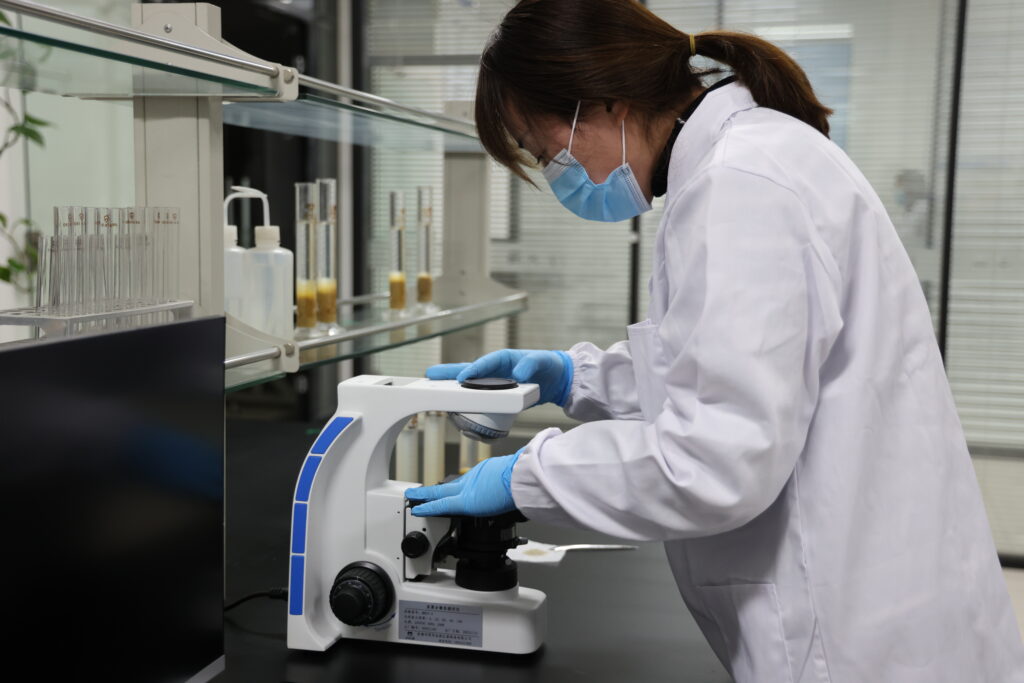
Which geomembrane to use for metal?
Choosing the right geomembrane for metal mining applications depends on various factors such as the type of metal being extracted, the chemical properties of the leachate, environmental conditions, and specific project requirements. Here are some commonly used geomembranes in metal mining, along with their characteristics:
High-Density Polyethylene (HDPE) Geomembranes:
- Durability: Highly resistant to punctures, tears, and chemical degradation.
- Chemical Resistance: Excellent resistance to a wide range of chemicals, including acids and bases commonly used in metal extraction.
- UV Resistance: Good resistance to UV radiation, making them suitable for exposed applications.
- Applications: Ideal for lining heap leach pads, tailings ponds, and waste containment areas.
Linear Low-Density Polyethylene (LLDPE) Geomembranes:
- Flexibility: More flexible than HDPE, allowing for easier installation and better conformity to uneven surfaces.
- Chemical Resistance: Good chemical resistance, though generally slightly less than HDPE.
- Puncture Resistance: Excellent puncture resistance, making them suitable for applications with rough substrates.
- Applications: Suitable for heap leach pads, tailings storage facilities, and secondary containment areas.
Polyvinyl Chloride (PVC) Geomembranes:
- Flexibility: Highly flexible and easy to install, even in complex or irregular shapes.
- Chemical Resistance: Moderate chemical resistance; may not be suitable for highly acidic or basic environments.
- UV Resistance: Typically less UV resistant than HDPE and LLDPE, often requiring protective cover.
- Applications: Suitable for temporary or short-term applications, small ponds, and secondary containment areas.
Ethylene Propylene Diene Monomer (EPDM) Geomembranes:
- Flexibility: Extremely flexible and easy to install.
- Chemical Resistance: Good resistance to a variety of chemicals, though not as high as HDPE.
- UV and Weather Resistance: Excellent resistance to UV radiation and weathering.
- Applications: Suitable for smaller-scale applications, decorative ponds, and some containment areas.
Geosynthetic Clay Liners (GCLs):
- Composition: Typically composed of bentonite clay sandwiched between layers of geotextile.
- Sealing Ability: Forms a low-permeability barrier when hydrated.
- Chemical Resistance: Effective for certain applications, but may require additional layers for highly acidic or basic conditions.
- Applications: Often used in combination with other geomembranes for enhanced containment, especially in tailings storage facilities.
Selection Considerations:
- Chemical Properties: Match the geomembrane’s chemical resistance to the specific chemicals used in the mining process.
- Physical Conditions: Consider the geomembrane’s durability, puncture resistance, and flexibility based on the site conditions.
- Environmental Factors: Take into account UV exposure, temperature fluctuations, and other environmental conditions.
- Project Longevity: Choose a geomembrane that meets the required lifespan of the project.
For most metal mining applications, HDPE and LLDPE geomembranes are preferred due to their superior chemical resistance, durability, and suitability for long-term use in harsh environments. However, the specific choice should be made based on a detailed assessment of the project’s requirements and conditions. Consulting with a geotechnical engineer or a specialist in geomembrane applications can help ensure the best choice for your specific needs.